Japanese 5 stars 12 October 2016
Interview with Traditional Japanese Cultural Artisans
An interview with the owner of Maruhachi-Goban-ten, the specialized Go and Shogi shop who offers a selection of Go and Shogi equipments crafted by skilled artisans.
Timeless Masterpieces: Board and Pieces Used in the Meijin Title Match
The other day, I posted an article here to share our news that we had purchased a set of Shogi board and pieces to be used in the third Kyoku of the 74th-term Meijin Title Match (“Kyoku” is suffix to count Shogi games.)
Good value has been added to the board and pieces, since they were used during the prestigious Meijin Title Match. It is true, but moreover those works are exquisite in themselves.
You may find yourself surprising to know how much craftspeople spend time and effort to make those masterpieces. Let’s see “how much” in an interview below!
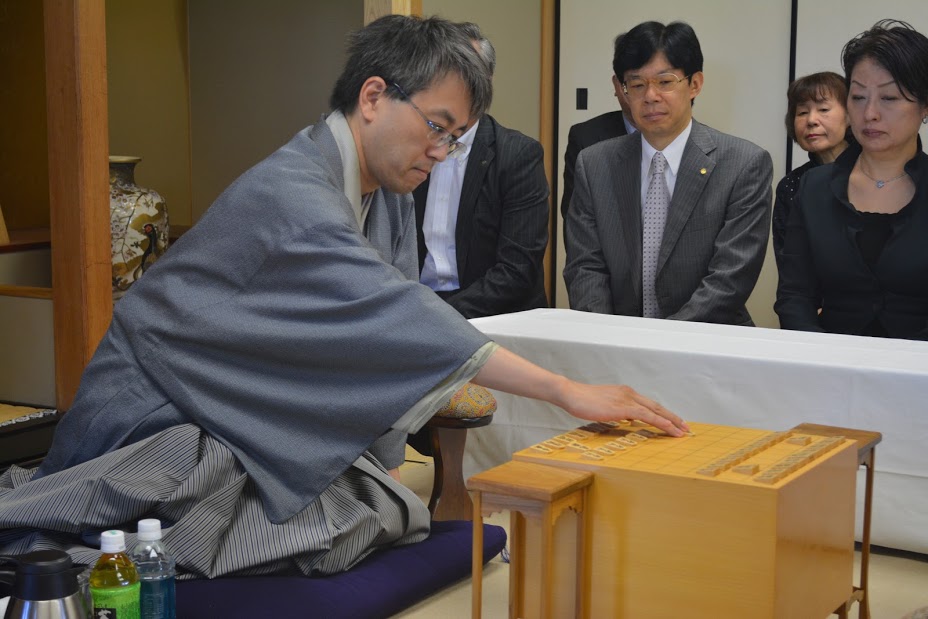
I had an interview with Mr. Tokujiro Kito who is the owner of Maruhachi-Goban-ten. Kito-san is also a younger brother of the late Mr. Atsuo Kito who was one of the certified master board maker [the title are recognized by Tokyo metropolitan government as “Governor Tokyo excellence skill person commendation.”]
Kito told me the process in which one log turns out to be a Shogi board and his brother’s dedication as a craftsman throughout this process.
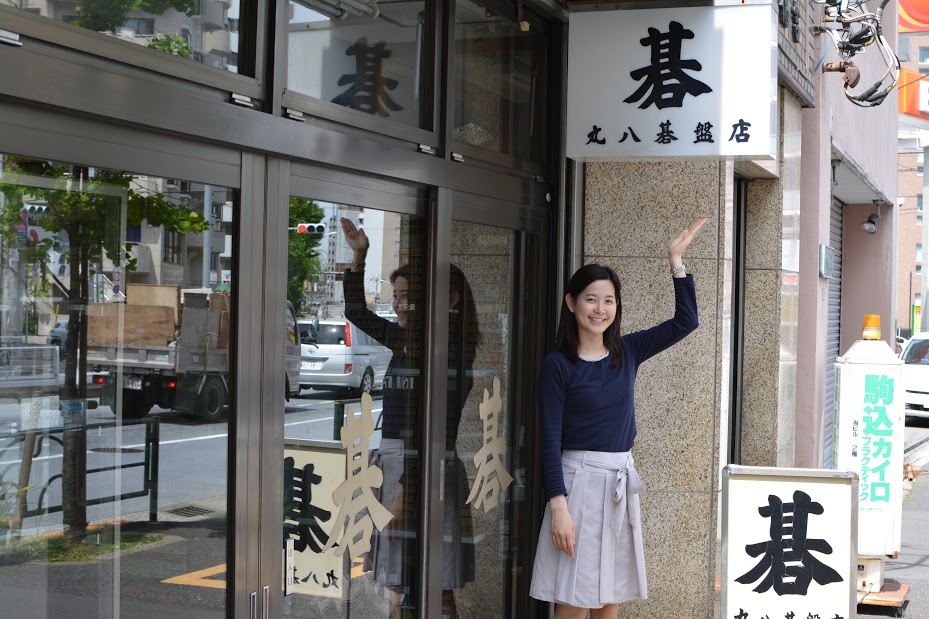
Shogi Board Transformed from a 300-Year-Old Huge Tree with 30 Years of Artisans’ Devotion
Ms. Akiko Nakakura (hereafter Akiko): What kind of tree did you use for this board?
Mr. Tokujiro Kito (hereafter Kito-san): The log for this board was from a huge tree grown in Niimi city in Okayama Pref. The board has the size of 7.5 sun board [“sun” is a Japanese traditional unit of length and suffix put behind a number to describe a quality of Shogi board in terms of its thickness]. Look at this. One corner of the board has the center part of annual rings. The board’s length is almost as the same as a half of the hemisphere of the log I used. Yes, as you have realized, the diameter of the log was that long! Even though it is well known that trees grown in Niimi, Okayama, typically have thick trucks, it is hard to find a tree trunk this thick. Inevitably the log was liable to be very expensive in itself.
Akiko: I see. You used very expensive and rare wood for this Shogi board. Now, could you tell me how to form the shape of a board from a log?
Kito-san: Yes. First, we cut box-shaped wood pieces (actually, Kito-san took Tofu as an analogy to describe the shape of cut pieces.) Then we keep them in a stock room for certain periods of time. During that time, since natural drying would cause cracks in the wood pieces, we need to coat them with several layer of paint. Say, we paint them from five to ten times. In addition, every two years we remove mold formed on their faces.
With regard to Shogi board, the thicker they are, the more appreciated in value. We could make only ten boards even from one large tree at the most. The rest part of the log will be processed to table boards or to board legs with gardenia shape.
Akiko: Only ten boards out of one high-quality log! I feel like that’s very wasteful.
Kito-san: Yes, it is. Besides the limited number of final products from an expensive log, we have to manage time-consuming processes. Working out for producing this board, we spent 20 years only to dry them and for the whole process 30 years was needed.
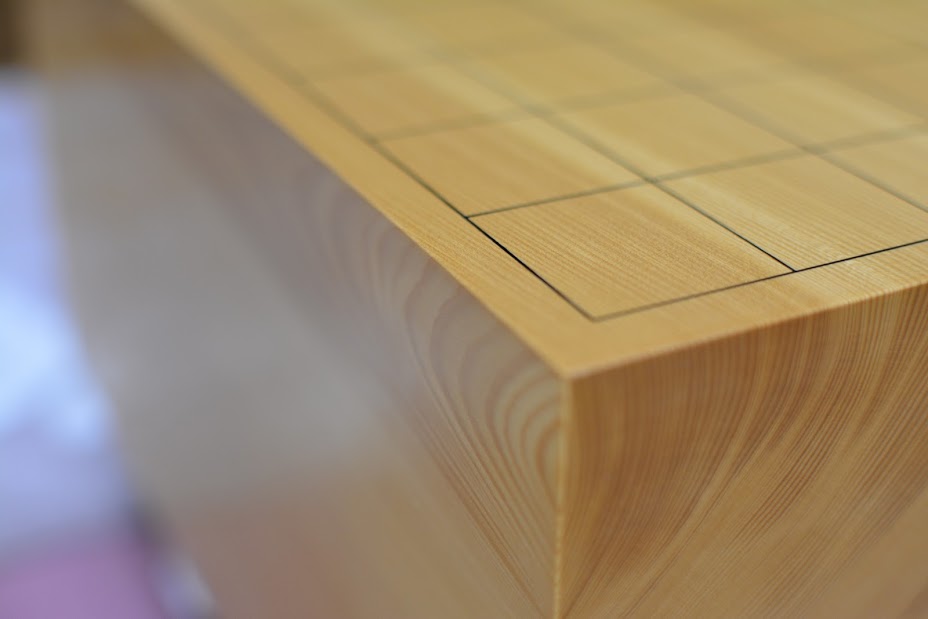
Dedication to Creating Crafted Shogi Boards and Pieces–the Spirits of Craftsmanship–
Akiko: 30 years is completely beyond my imagination! What do you think motivated your brother to expend a significant amount of time and effort in making boards?
Kito-san: Not only my brother, but my father also was one of the distinguished artisans in the truest sense of the word. I assume they had enormous pride as Go board craftsmen. (Go board craftspeople make Shogi boards as well.)
My father used to cut logs to make boards from early morning, around six or so, even on Sundays. My brother sometimes skipped school, looking for suitable woods for boards.
My brother was more skillful, and told me, “I take responsibility for crafting boards. You can engage in making something other.” I got complex from his words.
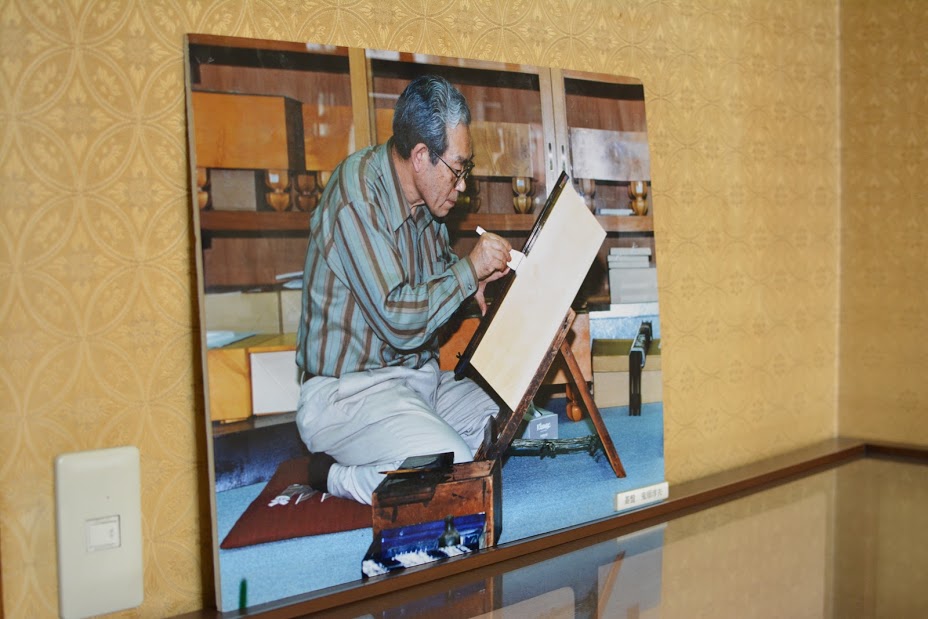
Akiko: What did you make then?
Kito-san: My brother devoted himself to making boards. Contrarily I worked hard to make Shogi pieces, not board. Dealing with small things suited my preference and abilities. In fact, my hobby was stamp collection when I was a college student. Oh, I remember one more. Assigned by Atsuo, I took care of our customers. He probably wanted to shut himself off from everything but creating boards as long as possible, I guess so.
Akiko: How do Shogi boards Atsuo and you made differ from other artisans’?
Kito-san: We, Maruhachi-Goban-ten, have been strongly sticking to high quality materials and put our whole soul into them. I believe the thing makes our products exceptional and unique is that. Indeed, the process of cutting board-shape pieces out of logs is relatively an easy part. We have to do something more to make our products exclusive.
In the present day, there are roughly two ways to produce Shogi boards: by machinery and by artisans’ own hand with care.
My father often said, “I can’t bear to watch logs cut by an electric saw.” “I feel sorry for them.” He insisted on hand working during the entire boards making process.
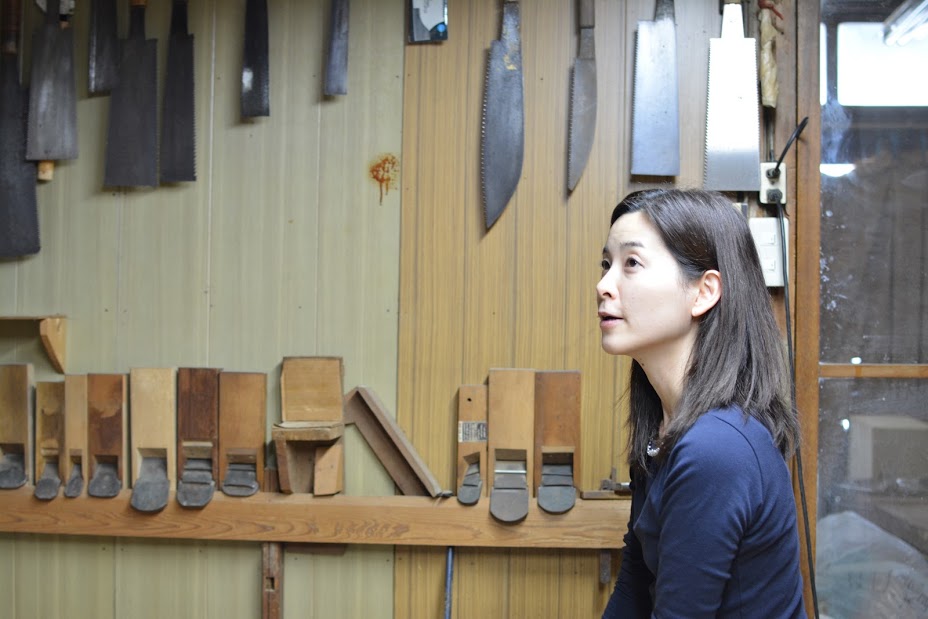
His style might not have been the only reason for why in those days all the artisans working at Maruhachi-Goban-ten were so skillful. Existing board makers scarcely craft legs of Shogi boards unless they use machine. Fortunately, we have enough stock of legs. My father got his artisans to produce certain amounts of crafted legs as a preparation for the time they all would be gone. We really appreciate my father and brother’s having such foresight. Although they have passed away, we are still able to deal in “our” Shogi boards.
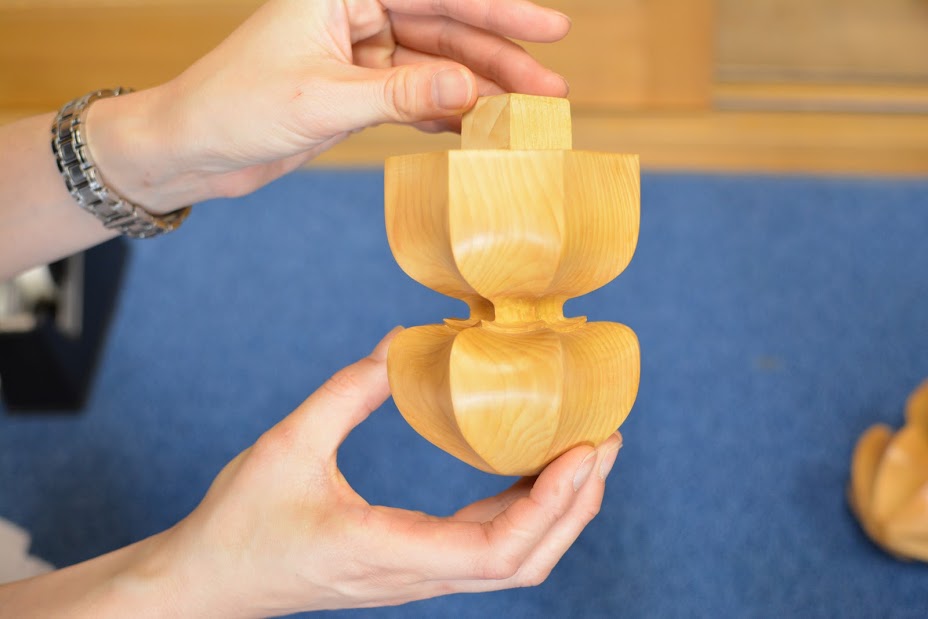
Akiko: I heard some craftspeople put their name on their works. It means that they do so because they create a board with great enthusiastic passion. Is it right?
Kito-san: We, Maruhachi-Goban-ten hardly ever put our name on our products. According to Japanese historical record, in the Azuchi Momoyama period, during the particular period when “Taiko Hideyoshi” unified the country [Taiko refers to a father of the Imperial], swords were regarded as tools to improve internal self. And then, Go boards were used when commanders planed strategies [presumably, Shogi boards were also used in the same way]. It was the age of civil wars; obviously no one left any footprints to reveal a battle plan. Having respect for history, we don’t put names on boards without our customers’ requests.
Akiko: I see. By the way, it seems that the marketplace has been swamped with cheap imports, such as Shogi boards and pieces made in China. Have you noticed that?
Kito-san: In my 20’s or 30’s, even expensive ones sold well, but not now. The market price of made-in-China board is much cheaper than made-in-Japan board. Japanese product is priced at several million yen, on the other hand Chinese one is at several hundred thousand yen. It’s understandable that people prefer to buy things at more affordable price. At the same time, it is also true that there are a certain number of people who have a concrete appreciation as to what constitutes high quality and purchase an expensive made-in-Japan board by preference.
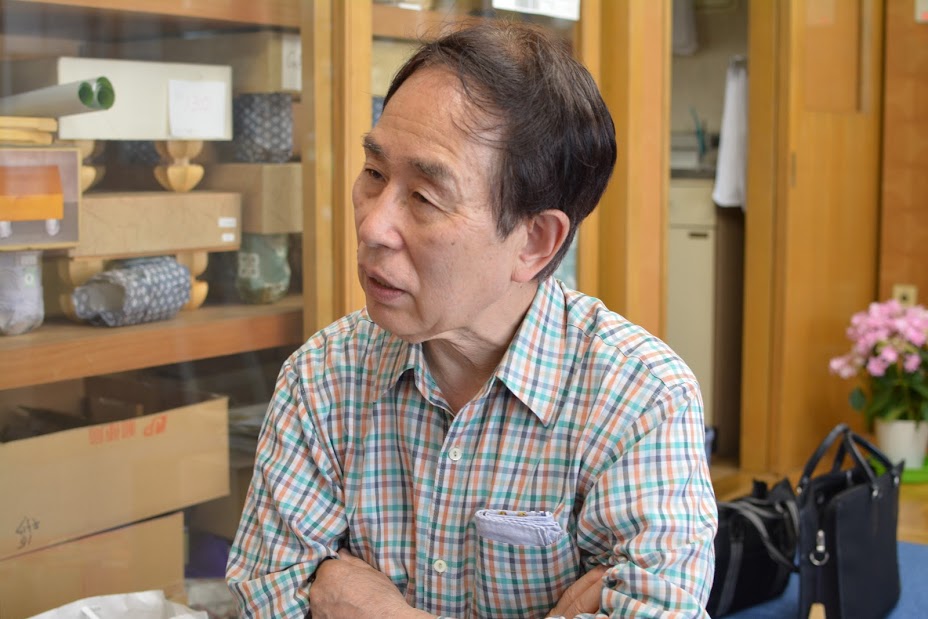
Postscript–after the Interview–
Having this interview, I reaffirmed craftspeople spend incredibly long period of time to produce exquisite Shogi boards. We can observe the history of a 300-year-old tree on the boards as beautiful grain patterns. I can’t so much as imagine about 300 years ago, but I have a feeling of closeness to ancient people.
Entire production process usually takes more than 20 years. 20 years is equivalent to the period from birth to adulthood. My oldest daughter is still 10 years old. There is a long road ahead! I’m wondering if board makers would feel like sending off their child when they sell their products made with delicate care and time.
Kito-san said over and over again, “My father and brother were master craftsmen in a real sense.” Now, Kito-san has passed masterpieces onto their customers. Authentic Shogi boards are masterpieces that have been passed down through generations from one person to the next while carrying craftsmanship. We are surely going to use the board from Kito-san very carefully for years to come.
We, the Nakakura family, had one Shogi board with legs. I used it to practice Shogi with my father and younger sister countless times in the past. Now, I have three boards with legs at home that my father in law bought. He has passed away already. Whenever I use these boards, they remind me of him. It may well seem a bit sad that one Shogi board with legs or one Go board per household is rare case. That’s all history now. However, there is no doubt that Shogi boards with legs will be used continuously in the Title matches. I sincerely hope that such Japanese traditional culture will always be preserved.
In closing, I would like to express my sincere thanks to the owner, Mr. Tokujiro Kito, and to all of Maruhachi-Goban-ten for your time and help.
Maruhachi-Goban-ten
http://www.maruhachigobanten.jp